Introducing a New Backpack Fabric: In Collaboration with Pertex
Known for their ultralight, high-performance fabrics in technical outerwear, we’ve once again teamed up with Pertex—this time to develop their first-ever backpack-specific materials: Pertex® 07RS-PC and Pertex® 21RS-PC.
Through regular development sessions, we worked closely to create original textiles that are both lighter and stronger than anything we’ve used before. The result is a fusion of Pertex’s deep technical expertise and our minimalist, ultralight-focused design philosophy.
These new fabrics will debut in Spring/Summer 2025, featured in updated versions of the ONE, MINI, and MINI2 packs.
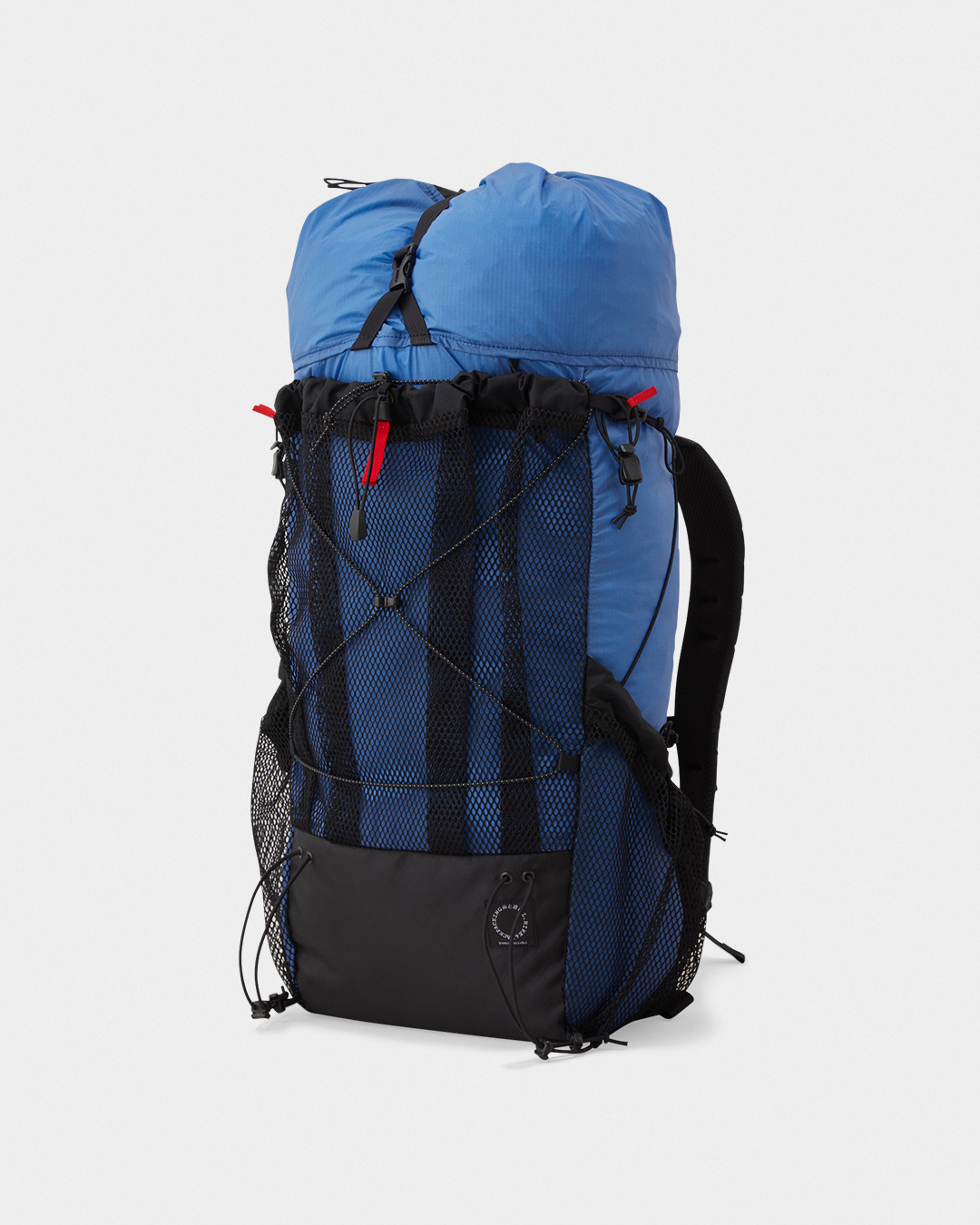
MINI2
Release: March 31st
Black, Classic Blue, Mustard, Slate Khaki
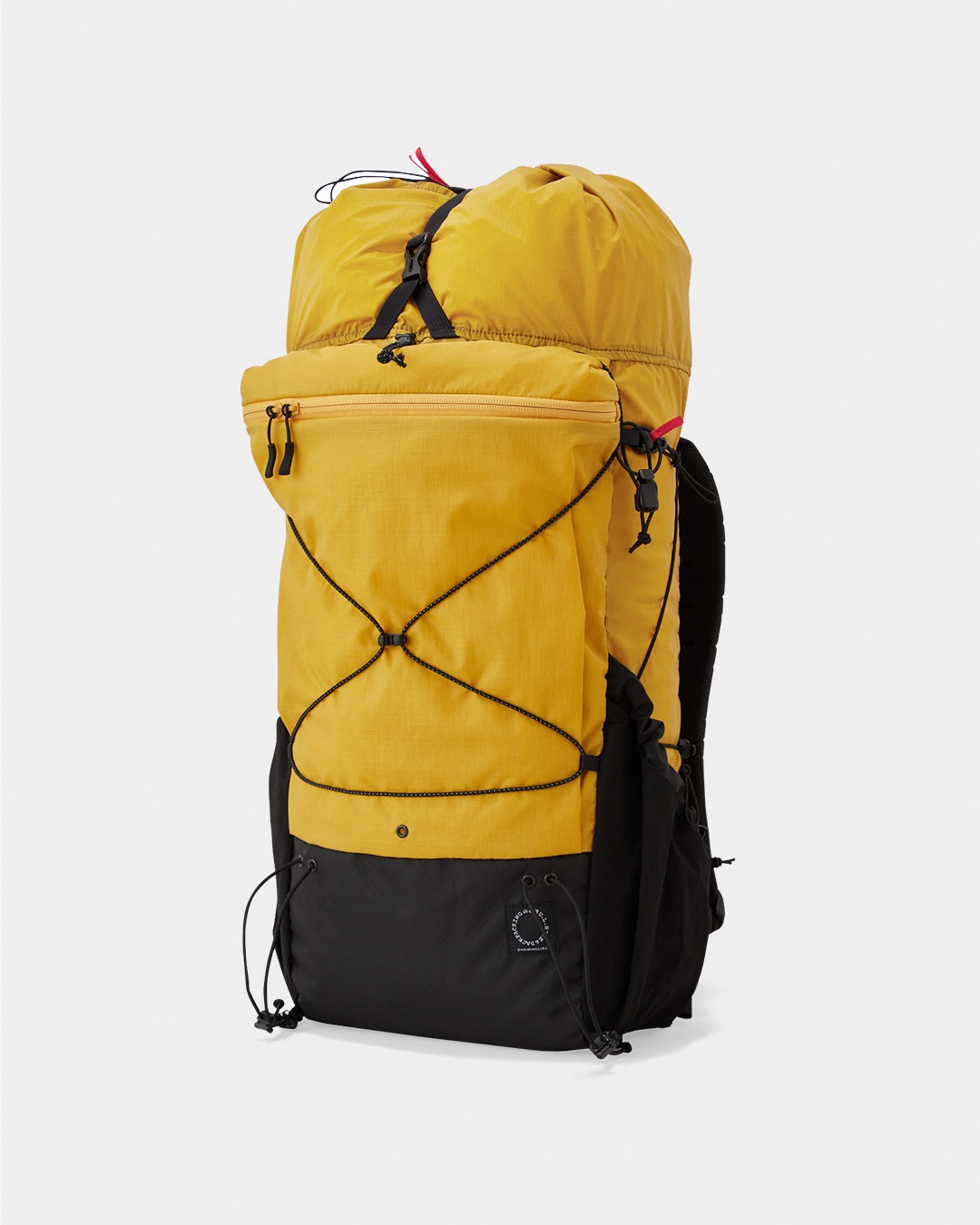
MINI
Release: May
Black, Classic Blue, Gray, Mustard, TS White
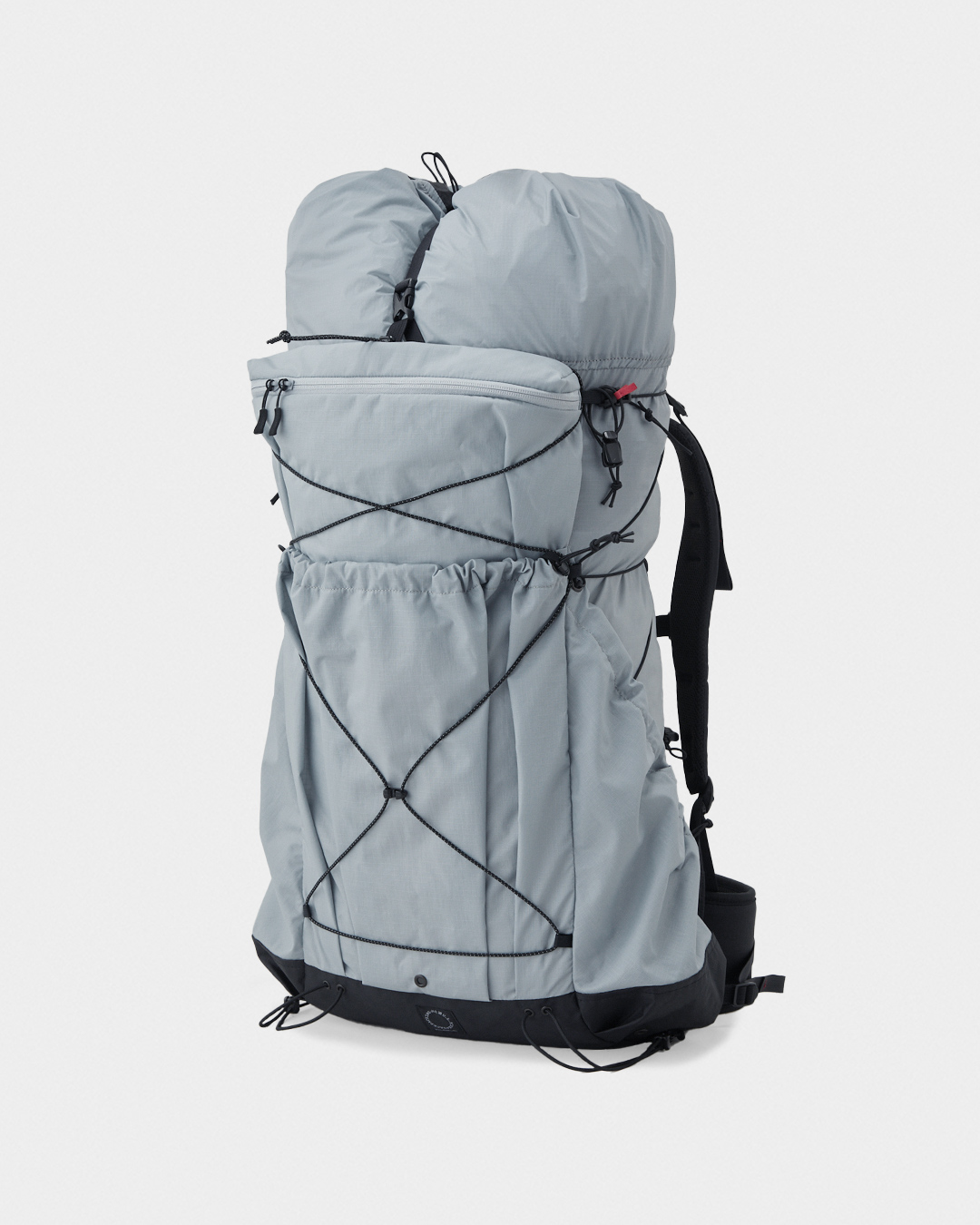
ONE
Release: June
Black, Classic Blue, Mustard, Gray, TS White
Fabric Highlights
- Despite being made entirely from nylon, the fabric achieves tear strength levels approaching those of UHMWPE (ultra-high molecular weight polyethylene)—a material known for its exceptional strength-to-weight ratio—and outperforms many other high-strength fabrics, including UHMWPE ripstop.
- A strategic mix of 210-denier and lighter 70-denier nylon is used throughout the pack, placing strength and weight savings where they matter most. For the base—where durability, waterproofing, and stain resistance are critical—we’ve used ECOPAK®, a fully waterproof material.
- All fabrics, including the main body and pockets, are dyed in the same facility to ensure consistent color tone and a clean, unified look.
About Pertex
Pertex is a high-performance fabric brand founded in the UK in 1979, now developed and managed by MN Interfashion in Japan. Known for its ultralight, tightly woven textiles, Pertex combines windproofness, water repellency, and breathability—qualities trusted by leading outdoor brands worldwide. Its fabrics are widely used in down jackets, sleeping bags, wind shells, and rainwear, with a growing focus on sustainable, user-centered design.
Product Story
Designing with Depth
To create a more thoughtful, collaborative approach to fabric development, we turned to Pertex with an idea: what if we made a fabric specifically for backpacks?
Meeting Pertex for the First Time
By the time I had become obsessed with hiking and before founding Yamatomichi, Pertex was already well-known as a go-to brand for lightweight, high-performance fabrics in technical outdoor gear. Our first real encounter came around the time we started Yamatomichi, when my wife and I visited a Pertex trade show.
We didn’t know that attendance was by appointment only. Completely unaware, the two of us just showed up without a reservation.
The staff seemed a bit surprised to see us at first—but rather than turning us away, they listened with genuine curiosity. Mr. Taka, the representative we spoke with, admitted later that we were the first people ever to show up unannounced. But he found our story interesting and gave us his full attention. He still laughs about it to this day.
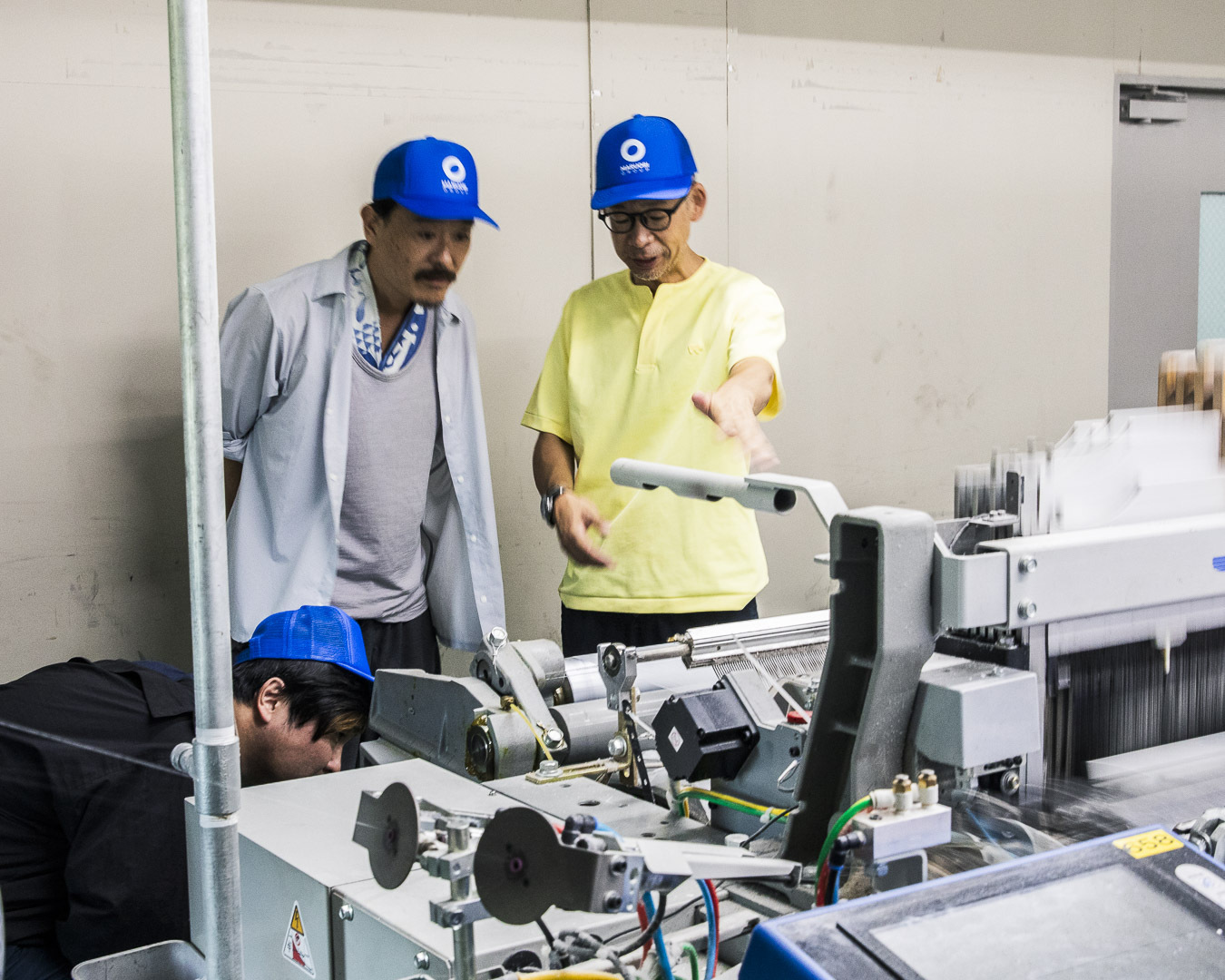
Right: Mr. Taka from Pertex. Left and center: Yamatomichi product team members Hirono and Nakagawa (photo taken during a factory visit).
We started by using existing Pertex fabrics, but things changed when we asked them to help develop a fabric for our DW 5-Pocket Pants. Taslan nylon, the fabric we were using at the time for our 5-Pocket Pants, lacked stretch and had a tendency to stick to the skin when sweaty. To solve that, Pertex created a custom fabric just for us.
Since then, we’ve worked with them to develop a range of original materials focused on lightness and function. Today, nearly every Pertex fabric used in Yamatomichi products is designed specifically for us.
An Idea Worth Weaving
At a Pertex trade show one year, while browsing their latest lightweight fabrics for apparel, we were once again struck by the depth and precision of their high-strength materials. That moment sparked a new idea—if Pertex were to develop a fabric for backpacks, it could lead to something truly unique.
A First for Pertex
Thanks to the trust built over years of collaboration, Pertex agreed to take on the challenge. It was a first for them—developing a fabric specifically for backpacks marked a completely new direction beyond their established lines like Shield or Quantum.
One of the most memorable decisions in the process was their choice to use nylon 6 instead of the typically stronger nylon 66. This allowed for a different balance of strength, texture, and weight. Additionally, by dyeing all components at the same factory, they achieved a consistent color tone across different fabric types—bringing visual unity to the final product.
The result is a fabric that goes beyond technical performance. It offers a refined handfeel and tonal richness that gives each backpack a distinct, elevated finish.
Through this collaboration with Pertex, we’re continuing to explore new and meaningful ways to approach design and materials.
More about the fabric
Backpack Material Comparison
Combining strength and lightness is no easy feat. By leveraging the unique properties of nylon 6, we set out to create a fabric that surpasses the strength of conventional backpack-grade nylon—without compromising on weight.
A precisely engineered weave and advanced coating technology give the fabric both flexibility and resilience, allowing it to absorb impact while maintaining long-term durability in the field.
Tear Strength and Fabric Weight
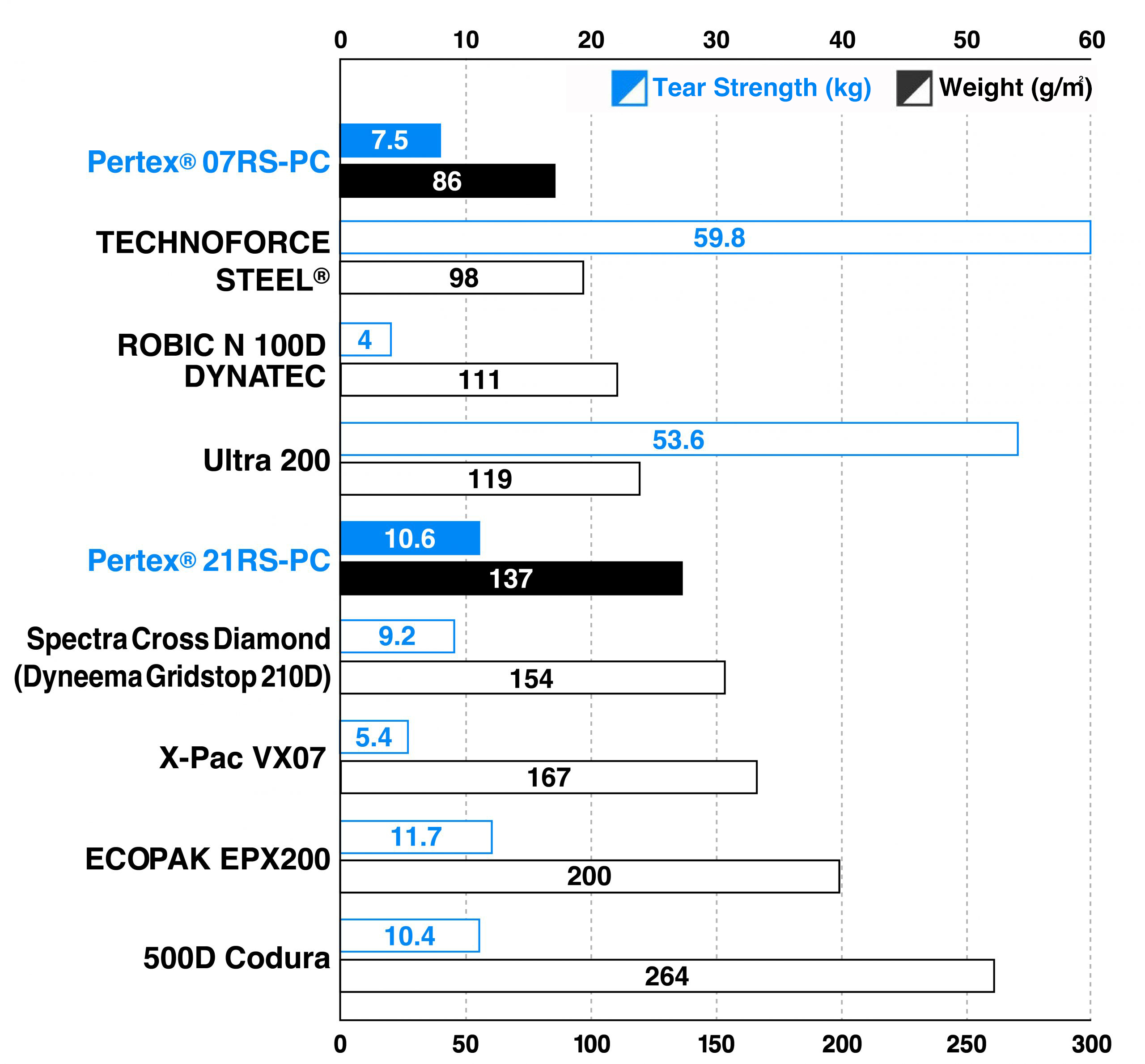
Tear strength (kg) represents the average of both vertical and horizontal measurements.
Fabric Strength Relative to Weight (kg per g/㎡)
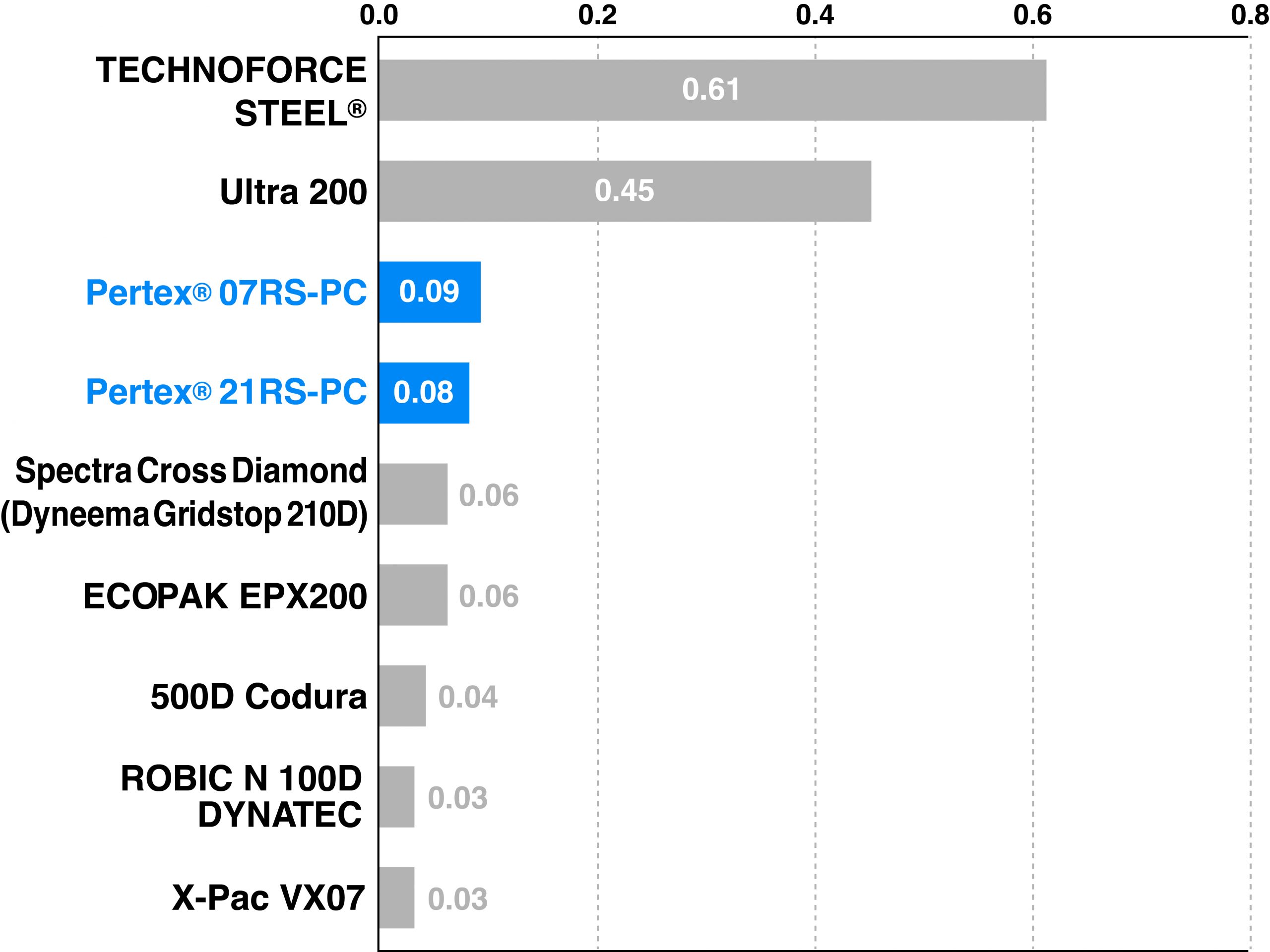
To highlight the relationship between weight and durability, the materials are ordered by tear strength per gram of fabric. The newly developed Pertex fabric ranks just below 100% UHMWPE (ultra-high molecular weight polyethylene) materials in strength—despite being made entirely from nylon.
Why Nylon 6—and Its Unique Performance
Pertex has worked primarily with nylon 6 since its founding, building a deep understanding of the material’s characteristics. While they do use nylon 66 when the application demands it, their fabric development is always based on selecting the right material for the intended function.
Nylon 66 is typically known for its high strength and abrasion resistance, but it tends to be stiff and more prone to sudden failure under stress. Nylon 6, by contrast, offers greater flexibility and can stretch slightly under load, allowing it to disperse impact more effectively. For this project, we chose to embrace the natural suppleness of nylon 6 and designed a fabric that is both lightweight and exceptionally strong.
A Balanced Weave Structure for Durability
To take full advantage of nylon 6’s flexibility, we carefully considered the fabric’s weave. While tighter weaves typically yield higher strength, they can also become overly rigid and more prone to tearing under localized stress. Instead, we adopted a slightly looser “open” weave structure that allows the fabric to better absorb and distribute force.
We also used the same denier of nylon 6 yarn for both the vertical and horizontal threads, giving the fabric consistent strength in both directions. This uniformity helps distribute pressure evenly across the surface and prevents stress from concentrating in a single area.
Balancing Strength, Water Resistance, and Dirt Repellency
Water resistance often requires tighter weaves and heavier coatings—but these come at the cost of flexibility and sometimes even durability. In developing Pertex® 21RS-PC (a 210-denier fabric), we explored a weave density that balances tear strength and weight while accepting moderate trade-offs in water resistance.
As a result, the fabric offers excellent durability while staying lightweight. However, its water resistance isn’t extremely high, and because of the more open weave structure, dirt can more easily work its way into the small gaps between threads. To address this, we chose ECOPAK® for the base of the pack—an area that demands both water resistance and stain resistance.
A Coating Designed to Last
Most nylon backpack fabrics use polyurethane (PU) coatings to improve water resistance and durability. But PU is prone to breaking down over time, especially with exposure to moisture and sunlight, often resulting in peeling or stickiness.
To overcome this, we used a polycarbonate coating—a tougher, longer-lasting option also found in car interiors, architectural panels, and industrial protective gear. It’s far more resistant to UV and humidity, making it a great fit for long-term outdoor use. That said, polycarbonate is more difficult to work with and more expensive than PU, which is why it’s still rarely used in textiles.
A New Challenge for Pertex
While Pertex has long specialized in lightweight materials for outdoor apparel, developing a fabric for backpacks was entirely new territory. They had limited experience working with 210-denier yarns, which added to the complexity of the project. With every step—from weaving to coating—they worked closely with us, testing and refining until we found the right balance.
This joint effort resulted in a fabric that opens new possibilities for pack design. And the collaboration doesn’t end here—together, Pertex and Yamatomichi will continue to develop high-quality backpack fabrics built to last.
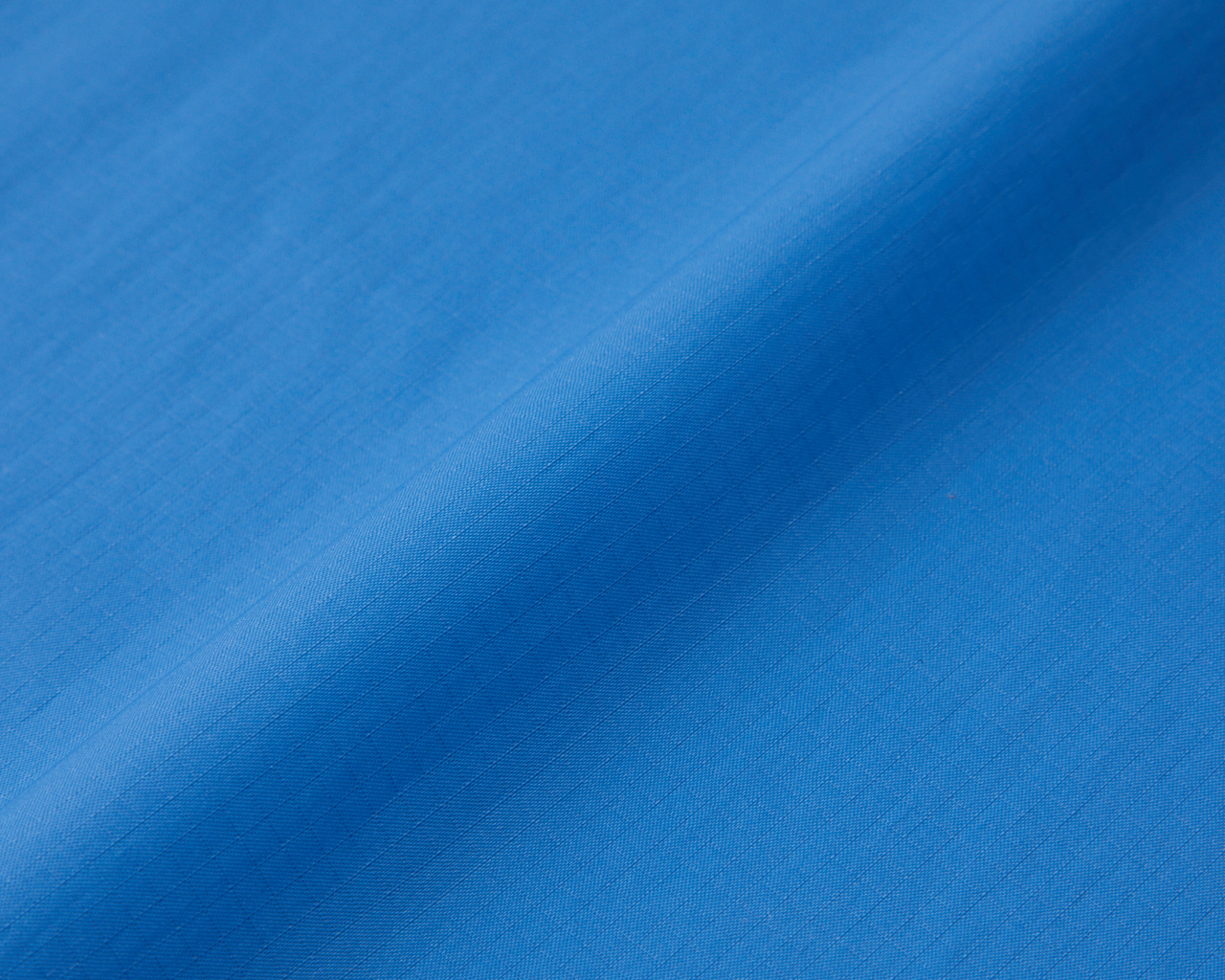
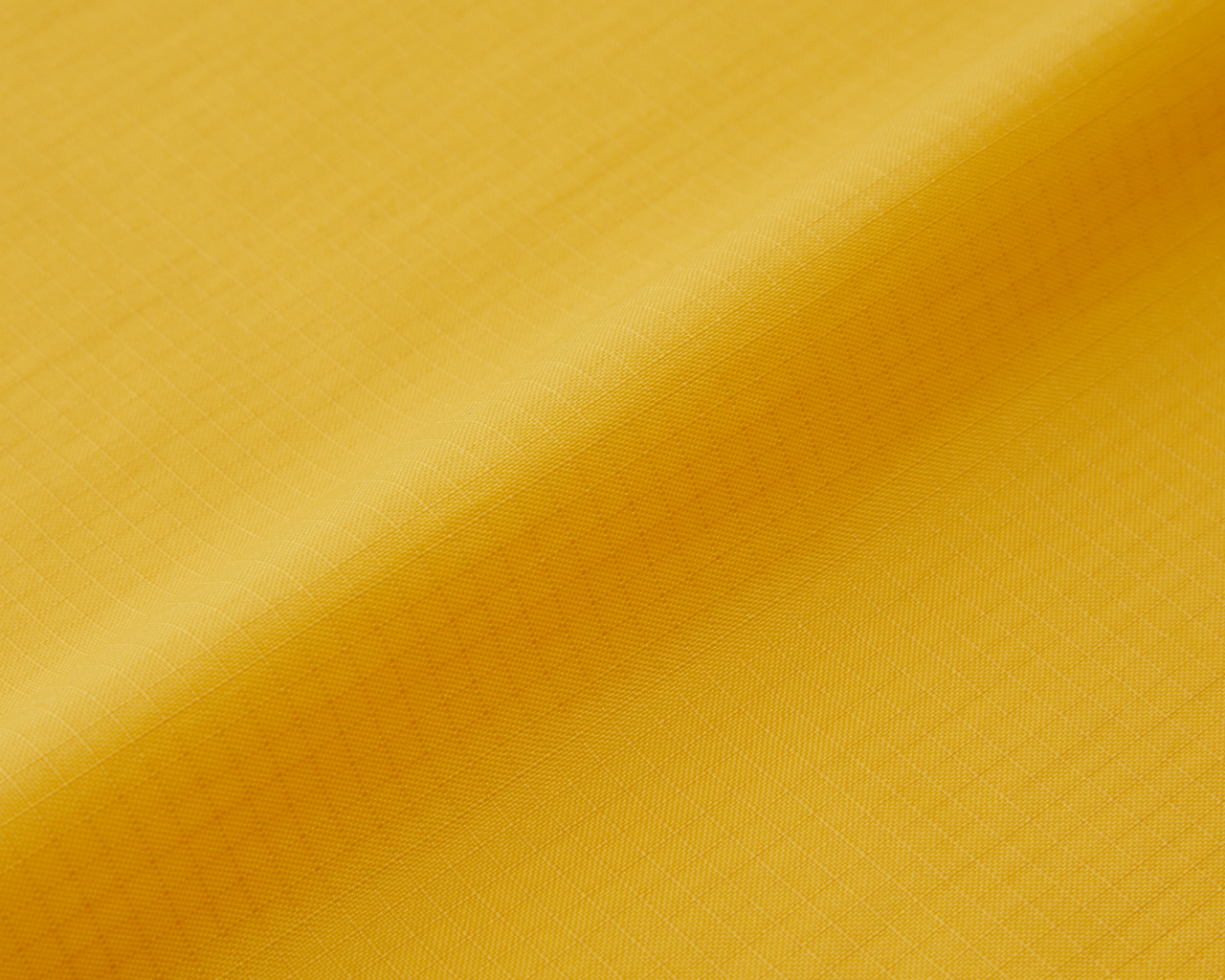