Revisiting Our Production System
Introduction
Yamatomichi has been producing almost all our products locally in Japan since we started out in 2011. We chose to manufacture our products locally so that we could be close to the production and handle any issues that might occur quickly. We always thought that in order to continue making good products, producing locally in Japan was the best option.
However, as we have grown, we are increasingly feeling the limitations of local production in terms of production capacity, capability and innovation. Local Japanese factories are currently facing various Issues such as an aging and diminishing workforce and are often reluctant to invest in new technology because of an uncertain business climate.
On the other hand, many overseas factories are much more progressive, invest in the latest equipment, have a stronger and younger workforce and surpass many Japanese factories in terms of production efficiency and quality. We decided to shift some parts of our production overseas to better understand and learn about overseas production and be able to continue to produce what we believe to be some of the best ultralight gear around.
Starting from 2025, Yamatomichi will manufacture a part of our products in Vietnam and Bangladesh. . We are doing so in collaborating with MN Interfashion Co. Ltd., the company that makes Pertex.
The back mesh panels for our backpacks will be made in Vietnam. The All-weather Alpha Jacket and our 5-Pocket Shorts and Pants made from Taslan nylon will be produced in Bangladesh. Both factories are highly reliable, handling products for renowned brands in Japan and around the world.
We are not expanding abroad solely to increase production but want to deepen our understanding and see what modern manufacturing has to offer. This way we believe we can further evolve manufacturing in Japan.
To this extent, we are currently planning to build a brand new factory in Kamakura. The building will integrate our current office, research facility, production, staff cafeteria and more.
Usually, factories are often built in rural areas or suburbs with lower land costs, but with this project, we want to make a factory in the center of Kamakura. We plan on sharing this journey with everyone as we enter this new phase of manufacturing, marketing, and community.
Parallel with exploring production overseas, we are also establishing a local production factory in Toyooka, Hyogo Prefecture to learn first hand about large scale production. Out hope is that the Toyooka factory will act as the training grounds for our future Kamakura factory employees.
We will continue to aim for the best quality in manufacturing.
We hope you will warmly watch our adventure to do so.
Akira Natsume, Yamatomichi Founder
Factory Tour
MN Interfashion Co., Ltd. representatives gave our product development team a tour around their factories. Here are the impressions of some staff members who participated in this inspection and what they felt and learned from this initiative.
Ho Chi Minh, Vietnam Factory
In Vietnam, we will be working with a factory that has manufactured backpacks for numerous outdoor brands. We will start by producing the mesh back panels of our backpacks.

Yumiko Natsume (Yamatomichi Founder and Backpack Development Manager)
Due to my job, I often handle backpacks from other companies for research, and many are made in Vietnam, sparking my interest in their high-quality sewing techniques.
We had the opportunity to visit a sewing factory in Vietnam, and seeing the scale, thorough quality control, and efficient production, I was inspired and learned a lot about how they produce high-quality products.
Ho Chi Minh was very hot in April, but the spacious and open environment was also memorable.
No matter the country, I realized again the importance of collaborating with trustworthy factories for manufacturing.
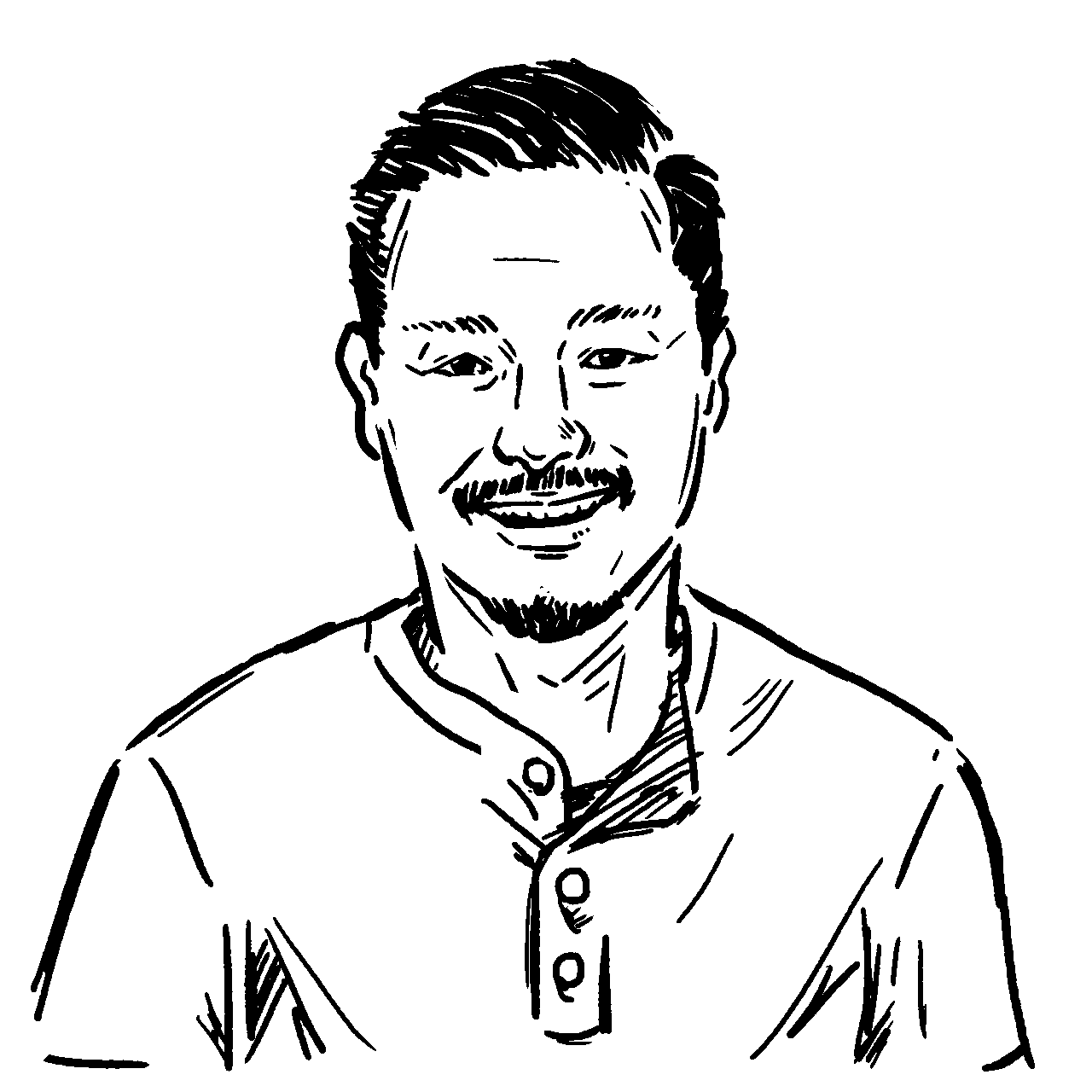
Takashiro Nakagawa (Production Management)
I had heard about backpack production in Vietnam from friends, but I realized that it varies greatly depending on the factory. It’s not about where you do it, but who does it. I was particularly impressed by the thorough inspection system at the factory. From fabric inspection, intermediate inspection during sewing, final inspection, and third-party spot checks by an independent department, the management system was meticulous.
Japan after the period of rapid economic growth shifted production to China, then Southeast Asia, then India, and next, perhaps Africa? Where will it go next? I also felt a sense of where things might head, but in an industry advancing with mechanization, what kind of manufacturing should we pursue?
Dhaka, Bangladesh Factory
A Japanese factory employing over 1,500 staff, mainly producing clothing for well-known outdoor brands and department stores. During our stay, we had many conversations and felt the founder’s strong commitment to manufacturing.
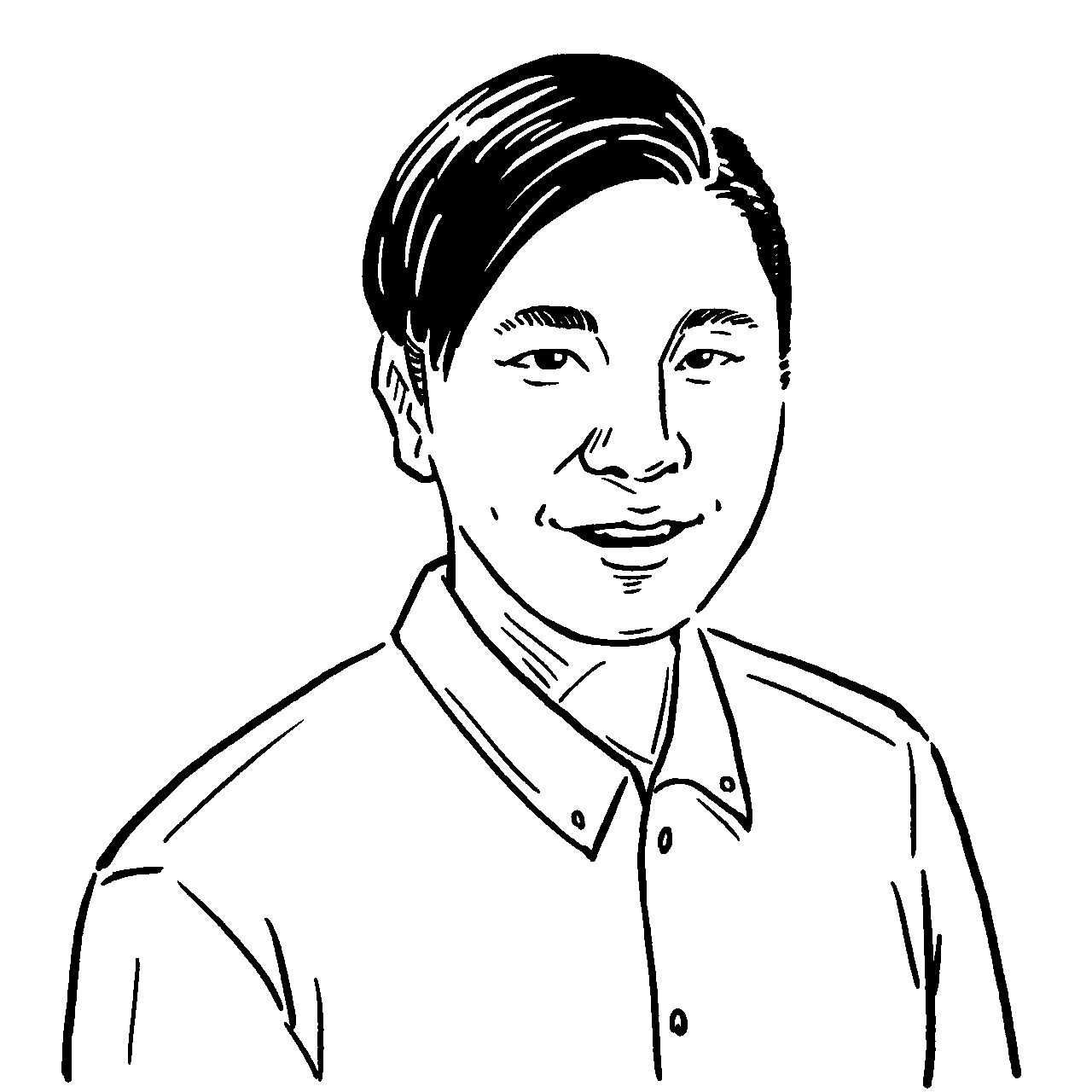
Hirotomo Hirono (Pattern Designer)
Many staff in the sample sewing team had received technical training in Japan, handling samples for various brands. The space, which could be called an atelier, was filled with people tackling each task carefully and facing their work seriously yet seeming to be enjoying it. It’s very important to align not just the technical aspects but also the “sensibility” part, which is often difficult to convey even locally in Japan . I had concerns about how this vague “sensibility” would be communicated overseas, but after several rounds of sample creation for production, I felt we aligned what we wanted to do with what could actually be done. I believe there is no single answer to “where and what is the best,” but I want to convey the atmosphere and enthusiasm felt during the overseas inspection to everyone involved with Yamatomichi
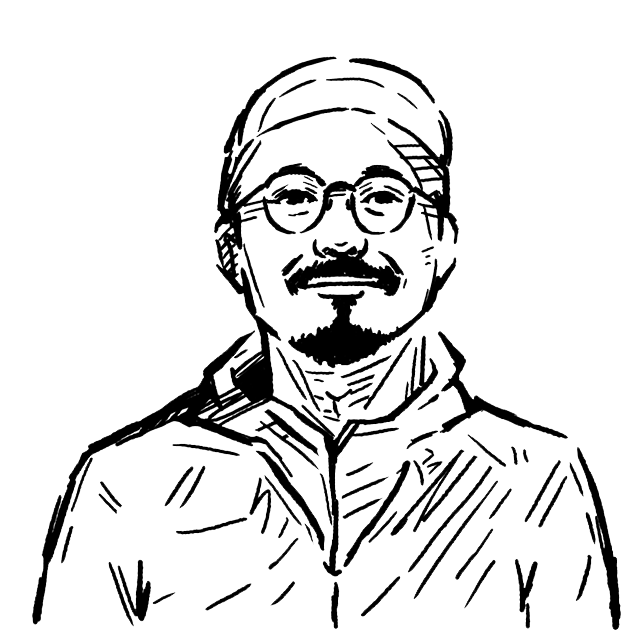
Akira Natsume (Yamatomichi Founder and Overall Supervisor)
My original impression of Bangladesh was not particularly good, especially after the 2013 Rana Plaza collapse, which killed at least 1,127 people in the worst accident in fashion history. However, visiting Bangladesh for the first time was a surprise. There were almost no tourists in Dhaka, the capital, and the locals were very friendly, with no aggressive sales tactics, creating a happy atmosphere. The factories were also excellent, and the representatives from MN and the factory staff were very impressive. Interacting with them and due to the character of the people, I grew to like this place. Seeing both the factories in Bangladesh and Vietnam, I felt again that the important thing is really about the people and not the place.